Key Components of a Lyophilizer
- vincenzo esposito
- Sep 10, 2020
- 2 min read
A typical lyophilizer, or freeze dryer, has nine main components plus axiliary systems to carry out the lyophilization cycle:
A vacuum chamber contains the shelves and the formulation to be lyophilized.
Hollow shelves hold the formulation and control its temperature.
Heat transfer fluid circulates inside the hollow shelves to precisely communicate cooling and heating through the shelves to the product.
Product to be lyophilized is specially formulated and typically contains the active ingredient, a solvent system, and several stabilization agents.
A condenser removes sublimated and desorbed solvent from the vapor phase by condensing or freezing it to maintain adequate vacuum inside the freeze-dryer. The condenser can be internally located in the chamber, or maybe a separate external unit communicating with the chamber through an isolation valve.
The mechanical or cryogenic refrigeration system provides refrigeration to the shelves and condenser (and sometimes the walls) of the freeze dryer by cooling the heat transfer fluid or directly expanding a refrigerant in the space to be cooled.
A heater provides heat to the HTF to slowly sublimate the ice and desorb solvent from the frozen cake on the shelves.
The vacuum pump pulls vacuum in the chamber and condenser.
Control hardware and software systems direct various parts of the complex freeze drying equipment and carry out the preprogrammed lyophilization cycle.
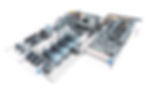
In addition, auxialiary systems provide capabilities including:
Cleaning and sterilizing the lyophilizer: SIP and CIP systems.
Auto-load and unload system.
Supplying extra or significant backup power, cooling water, and lubricant for the mechanical refrigeration system, and lubrication for the mechanical refrigeration system.
Supplying liquid nitrogen (LN2) to cryogenic system, which includes an insulated LN2 tank and piping to the refrigeration skid (mechanical systems do not need these).
All these systems must work together seamlessly to ensure desired end-product quality.